The Achilles’ heel of Estonian industry is low efficiency. Companies are struggling – many have already automated and robotized most of their production, yet they still lag behind manufacturers in Western Europe and Asia. The labor productivity of Estonia’s industrial sector is only 58% of the EU average.*
A company’s competitiveness increasingly depends on its ability to use artificial intelligence (AI). However, transitioning to AI is much more complex than simply automating a single job. Below, I outline the first steps that any industrial company can take to begin the process.
Start by collecting data
To fully leverage the potential of artificial intelligence, the AI solution must be able to continuously learn from the data generated within the company. That’s why the first step is data acquisition – carefully planning how to capture and store all data from every stage of the production process in a data warehouse.
Data collection must be automated – either by the production line itself or with separately installed sensors. Data accuracy is crucial; for example, it is important to distinguish between time spent setting up the line and time spent on actual production. Manually entering production data is therefore unsuitable, as it can lead to errors and inaccuracies.
The data gathered from production is used to regularly update the AI, since production changes over time – and so does the data. Depending on the dynamics of the company, an AI solution might need to be updated once a day, once a week, or even several times an hour. Buying AI is not like purchasing a traditional software package – it’s about setting up a self-learning system within the company.
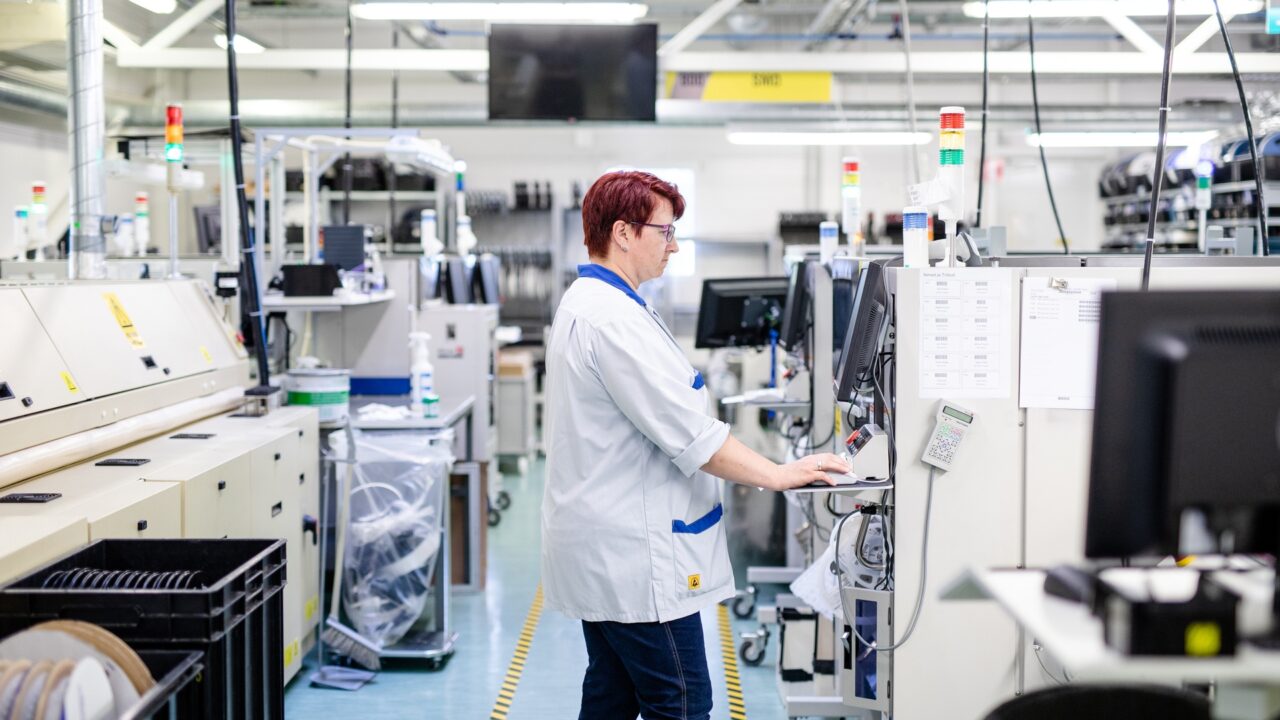
Electronics industry in Saaremaa. Image is illustrative | Photo: Renee Altrov
AI delivers the greatest value through process transformation
The second step is understanding that it’s not enough to simply add technology – processes themselves must be restructured. The last major technological leap in industry came with the introduction of robotics and automation. That was relatively straightforward: companies identified labor-intensive tasks and replaced them with automated solutions.
Using artificial intelligence in industry is not just about improving a single step in the production process. Real efficiency gains come from using AI to manage and orchestrate both production and business processes. This, however, requires a fundamental reorganization of current workflows – and much of the potential for efficiency lies outside of machines and production lines.
When visiting Estonian manufacturing companies, I’ve noticed that low-tech workflows – such as order management, production planning, quality control, and forecasting – consume a large portion of resources. As a result, overall productivity remains low.
With AI-driven management, these processes can be automated. For example, when a company using AI makes a new offer or accepts an order, it has already begun planning production and can accurately calculate the order’s cost, raw material requirements, and timing. The processes become more technologically complex – but logically much simpler.
Real-time process control is a competitive advantage
The third step is adapting to changes in real time. With AI-based production management, even frequent disruptions – such as order cancellations, line failures, delivery delays, or employee absences – don’t require extensive manual rescheduling, as the AI can do the work of multiple planners in seconds or faster. Updating a production plan 20 times a day is no longer a problem but a competitive edge, enabling high efficiency and productivity.
While many companies already use AI for quality checks on the production line – such as detecting and removing defective products – few are able to manage quality across the entire production chain.
Quality management means understanding the root causes of defects, learning from them, and preventing similar issues in the future. In other words, it’s about monitoring and improving process quality. This used to be possible only for companies with the resources to hire data analysts and perform high-level data collection. AI has now made this significantly more accessible and can identify the complex root causes behind quality issues.
For example, in the food industry, a one-degree temperature difference in one step or a slight moisture variation in another might not affect the product individually – but together, they can cause quality problems. With proper data collection and AI-driven quality control, it’s possible to identify such patterns and adjust production to prevent future errors.
Quality assurance has evolved from a final inspection step into a continuous goal throughout the entire production process.
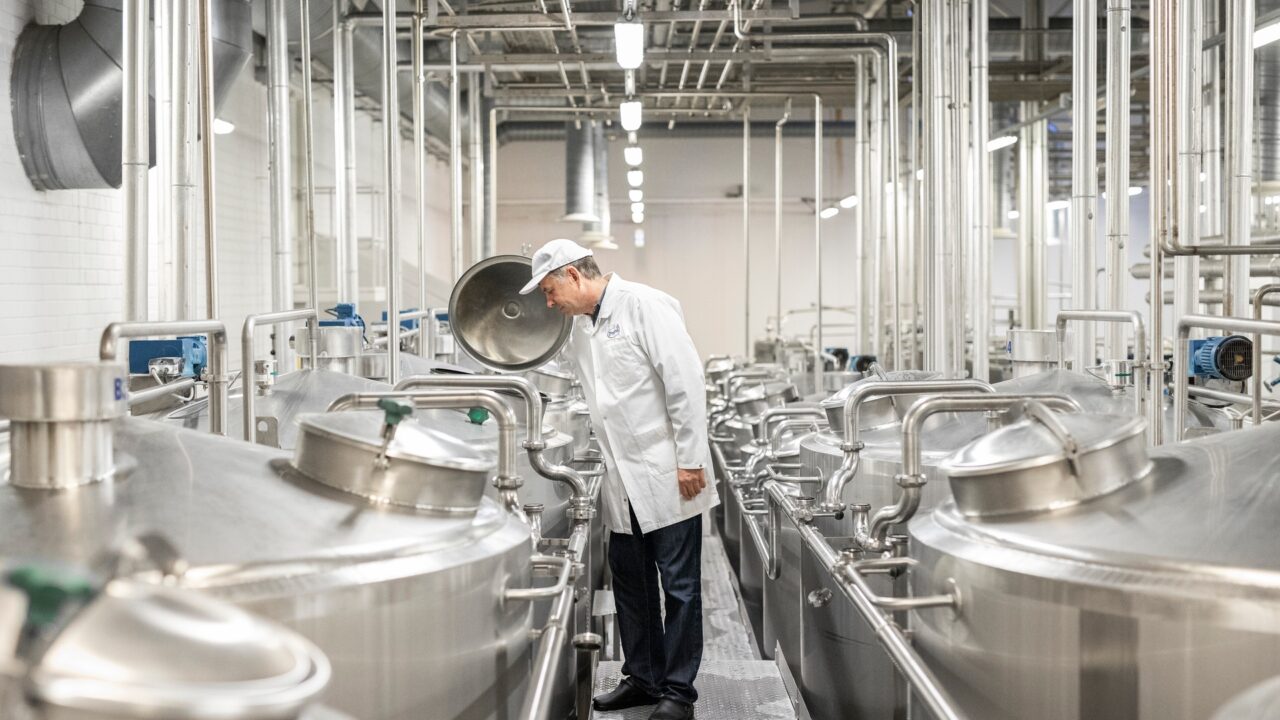
Dairy industry in Estonia. Image is illustrative | Photo: Renee Altrov
The big picture
Based on the experience of companies that have used AI consulting, I can say that it’s wise to start with a big-picture plan, but begin by changing one specific step in the production or business process. If the company’s main issue is production planning, it might be worth integrating the sales process and production management into a single AI-driven system. If the problem lies in quality control, consider addressing it in conjunction with managing a specific production line.
Once a smaller issue is resolved, the solutions can be connected. For example, data collected during quality control – such as production line speed and product parameters – can later be used to more accurately predict the time and cost of producing similar products.
The AIRE Centre for Artificial Intelligence and Robotics is dedicated to boosting the competitiveness of Estonian industrial companies by helping them adopt AI and robotics solutions.
AIRE aims to bring universities closer to industry and offers companies innovative custom solutions not typically available on the private market – including technology and software testing, data analysis methods, cloud solutions, predictive maintenance, and digital twin development.