My previous position was in the bio-based industries unit that coordinated the work of the joint undertaking between the European Commission and the Bio-based Industries Consortium – now known as the Circular Bio-based Europe Joint Undertaking. My tasks included analyzing the sustainability of biomass, based on the premise that demand for biofuels and bioproducts would continue to grow.
I reviewed over a hundred studies, which showed that during periods when widespread biomass use was projected, the global availability of usable biomass was estimated to be roughly twice as high compared to times when bio-based products were not seen as serious competitors to fossil fuels. The conclusion: when interest deepens, humanity tends to discover additional bioresources.
Before the last decade shift, the general mood around biomass utilization was rather pessimistic. The main area of use – bioenergy – faced dim prospects due to the rapid rise of renewable electricity. Global investments in liquid biofuel production, which peaked at over $25 billion in 2006 and 2007, dropped dramatically.
However, it might be more accurate to say that the sky above what was seen as “scarce” biomass began to clear. The broader picture was reshaped by the uptake of electric vehicles and the promising future of solar and wind energy. “Biomass” was released from the expectation of having to meet the world’s energy demand – especially since even growing needs could not have been met by the planet’s resources alone.
Now that biomass is no longer at the center of energy strategies, discussions about its adequacy are gradually fading. In forest-rich Estonia, there is still enough woody biomass available even when nature protection areas are excluded. The main issue is not about quantity, but direction: shifting from burning wood to producing bioproducts.
Graanul Invest, Europe’s largest wood pellet producer and an Estonian company, will eventually have to scale back its longstanding business as market demand declines. Wood-burning heating systems are gradually being replaced by heat pumps as technology advances and electricity prices fall.
In the UK, the last coal plant was closed at the end of September, and attention is now turning to the country’s largest power station, Drax –Europe’s leading consumer of wood pellets, primarily imported from the U.S. In Denmark, where pellets are also burned in large volumes, the final phase of the energy transition is expected after new offshore wind farms come online. Energy giant Ørsted closed its last coal plant last autumn, and only one remains operational in the country.
The phase-out of wood burning in large power plants is a logical step on the path to reducing air pollution. For Graanul Invest, this trend comes as no surprise – their €250 million investment to convert the Langerlo coal plant in Belgium to wood fuel ended in bankruptcy in April 2017 due to local opposition.
The phase-out of wood burning in large power plants is a logical step on the path to reducing air pollution.
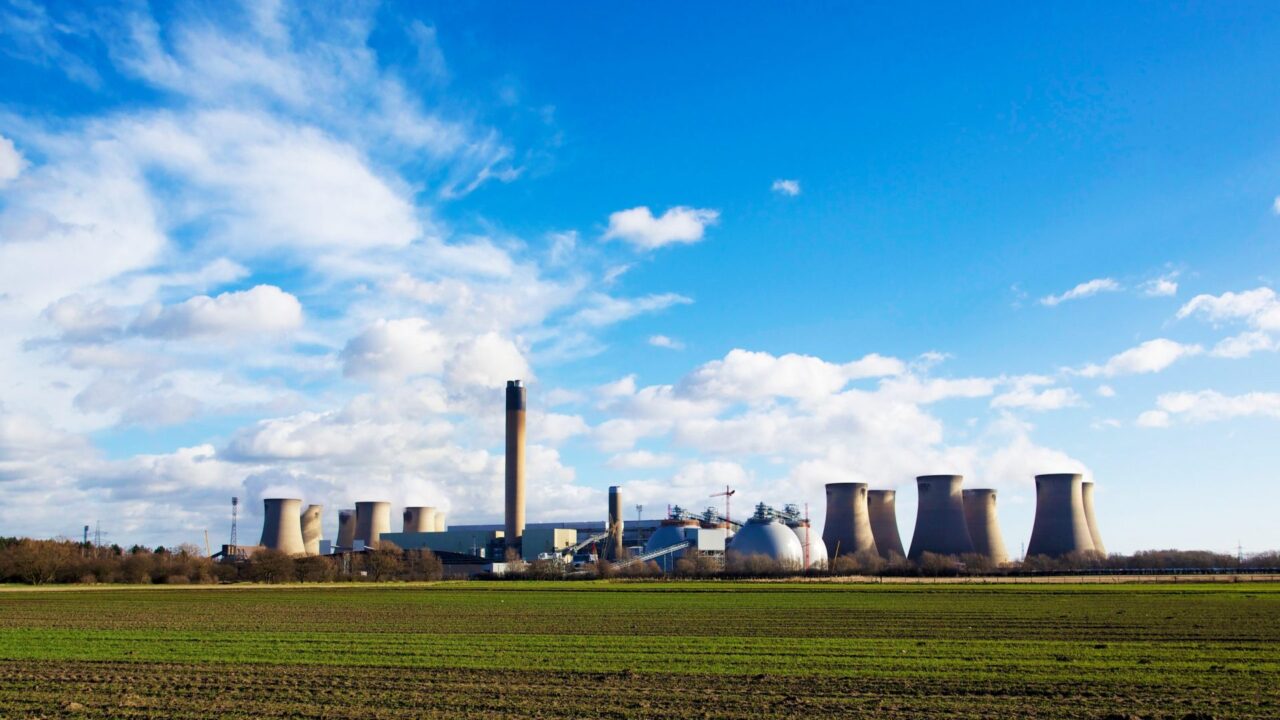
Drax power station in the United Kingdom, Europe's leading consumer of wood pellets. Photo: Drax UK
Black swan – or in Estonia’s case, the black stork?
Investment failures caused by exceptional events are often described as black swan appearances. Lauri Ulm, project lead for Enefit Green’s most important investment – the Sopi-Tootsi wind farm – recalled how the discovery of a black stork nest nearby led to sleepless nights: “Luckily, it turned out to be unused and unsuitable for nesting.” In Estonia, the black stork, capable of unexpectedly nullifying all efforts, might in fact be a more fitting symbol than the swan.
For advocates of bio-based industry, the unexpected opposition in Tartu to the construction of Estonia’s own large-scale biorefinery came as an unpleasant surprise. Although rational arguments against the plant quickly ran out, one trump card remained: the smell. Indeed, the production of wood sugars can be noticeable at close range, but the more modern the facility, the less any odor lingers. Today, every component of wood is utilized, and to detect any smell, one would likely need to step through the plant’s gates.
Just as with wind farm development hurdles, Estonia’s biorefining sector has effectively lost a decade. Fibenol’s decision to build its first full-scale plant just south of Estonia should be seen in the context of the prolonged debates in the Tartu region.
There are role models to look up to when making decisions
Finland has been advancing biorefining for years, achieving internationally significant results and establishing over ten plants. The Finns were also among the pioneers in biofuel production (Neste), gaining valuable experience in navigating political shifts. Despite shrinking markets for biofuels in the coming decades, production continues – particularly for marine and aviation fuels, where demand is expected to remain.
Much like in the wind energy sector, our northern cousins have pressed forward steadily in developing bioproduct facilities. The only major setback has been the closure of border-area plants dependent on Russian wood.
During the now-famous “Tartu saga,” Finland was frequently cited as a role model, especially the Metsä Fibre bioproduct mill in Äänekoski, completed in 2017 at a cost of €1.2 billion. The latest addition to this lineage is the Kemi bioproduct mill, inaugurated by Finland’s president on 23 October, though it had already begun production a year earlier. Metsä Fibre’s largest investment to date, this €2 billion project is expected to generate around €500 million in annual tax revenue and a similar increase in exports for Finland.
Finland has been advancing biorefining for years, achieving internationally significant results and establishing over ten plants.
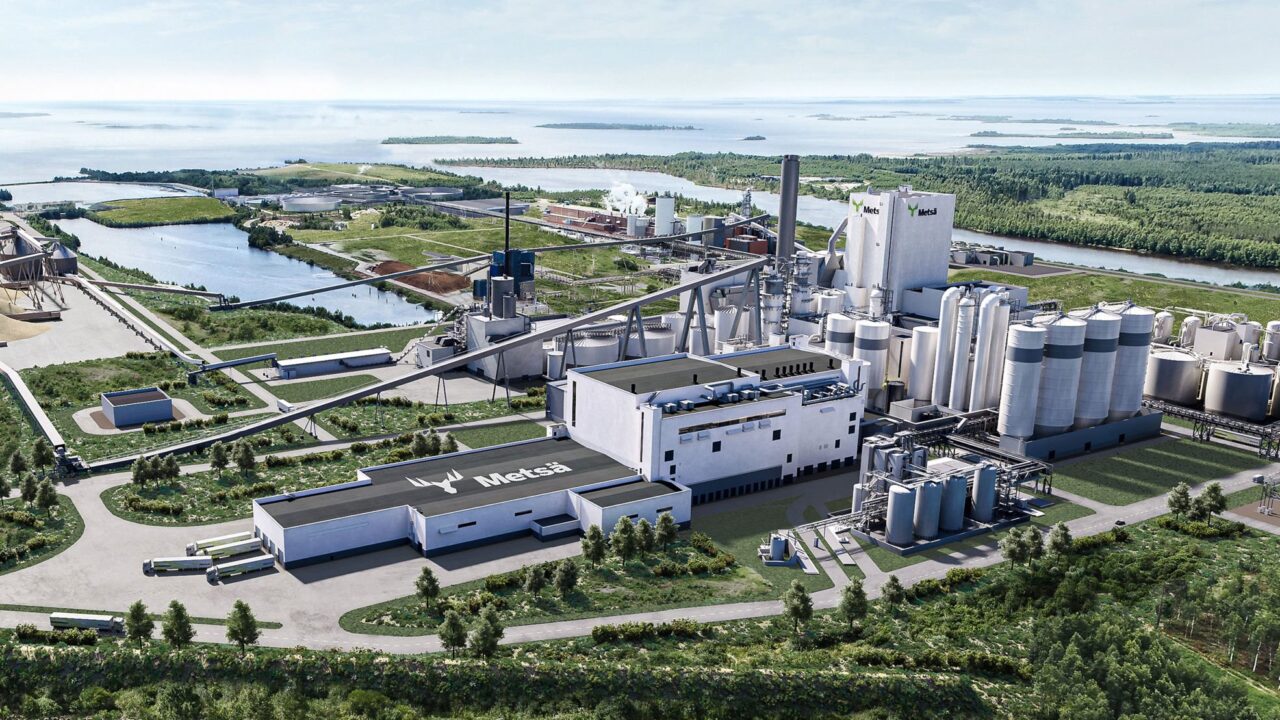
The Metsä Group's Kemi bioproduct plant, owned by 90,000 Finnish forest owners, was inaugurated on the Lapland coast in October. | Photo: Metsä Group The Metsä Group's Kemi bioproduct plant, owned by 90,000 Finnish forest owners, was inaugurated on the Lapland coast in October. | Photo: Metsä Group
The main bioproduct of both plants remains cellulose, used to manufacture consumer paper and cardboard. By-products such as tall oil and turpentine can be compared to crude oil – Metsä’s partners separate different-use fractions from the complex mix of liquid molecules. This creates a diverse industrial ecosystem around Metsä’s bioproduct mills, strengthened by a €20 million grant through Fortum and the Business Finland program.
Around the major companies, nearly a hundred partners have gathered to develop their own products through mutual support and collaboration. True, it may still take years for these partners to bring their products to market.
At the same time, smaller developers received an additional €50 million in support from the Finnish government. A standout example of R&D and startup innovation is the production of textile fibers from wood – the most well-known application being a dress worn by the Finnish president’s spouse at the Independence Day reception. Last spring, construction began on a textile fiber production unit adjacent to the Metsä bioproduct mill.
In addition, the French environmental services company Veolia is currently building a methanol plant next to the Äänekoski mill to purify by-products from the cellulose production process. Lignin – the “glue” that binds wood’s cellulose fibers – also offers broad application potential. A lignin refining demo plant using cutting-edge scientific research is scheduled to open in Äänekoski within a year.
The Äänekoski plant produces 1.8 terawatt-hours of electricity per year – 250% more than it consumes – with a generating capacity of 260 megawatts. The newer Kemi bioproduct mill has a slightly higher output of 2 terawatt-hours annually. Both plants generate nearly as much electricity as Estonia’s 300-megawatt nuclear reactor project, which has received political support but would consume a portion of its output internally.
Together, two bioproduct mills could offer a viable alternative to a nuclear power plant in Estonia. The key would be finding a solution that allows all steam to be redirected toward electricity production during calm winter weeks with little wind, while focusing on bioproduct manufacturing during summer periods when cheap electricity is abundant.
Such a solution would avoid the need to hire dozens of regulatory officials and allow scientists and lecturers to focus on better utilizing Estonia’s forests rather than developing nuclear expertise. Moreover, the Kemi bioproduct mill aims to achieve zero waste by the end of the decade – an undeniable advantage over a nuclear power plant.
Together, two bioproduct mills could offer a viable alternative to a nuclear power plant in Estonia.
Bioproduct development in Finland is led by the applied research center VTT, which secured as much funding from the previous EU research and innovation program Horizon 2020 as all Estonian institutions and companies combined. Starting this year, VTT is also the only European participant in two U.S. National Science Foundation global centers programs focused on biomaterials and food.
VTT’s Bioruukki pilot facility specializes in bioproduct development – a site I had the chance to visit at my own expense last spring. The facility offers companies and startups a wide range of equipment to refine their bioproducts and optimize production processes. This enables smarter decisions before investing in expensive production technology. In addition to numerous testing units, developers benefit from expert advice and support, making the development process more efficient and less risky.
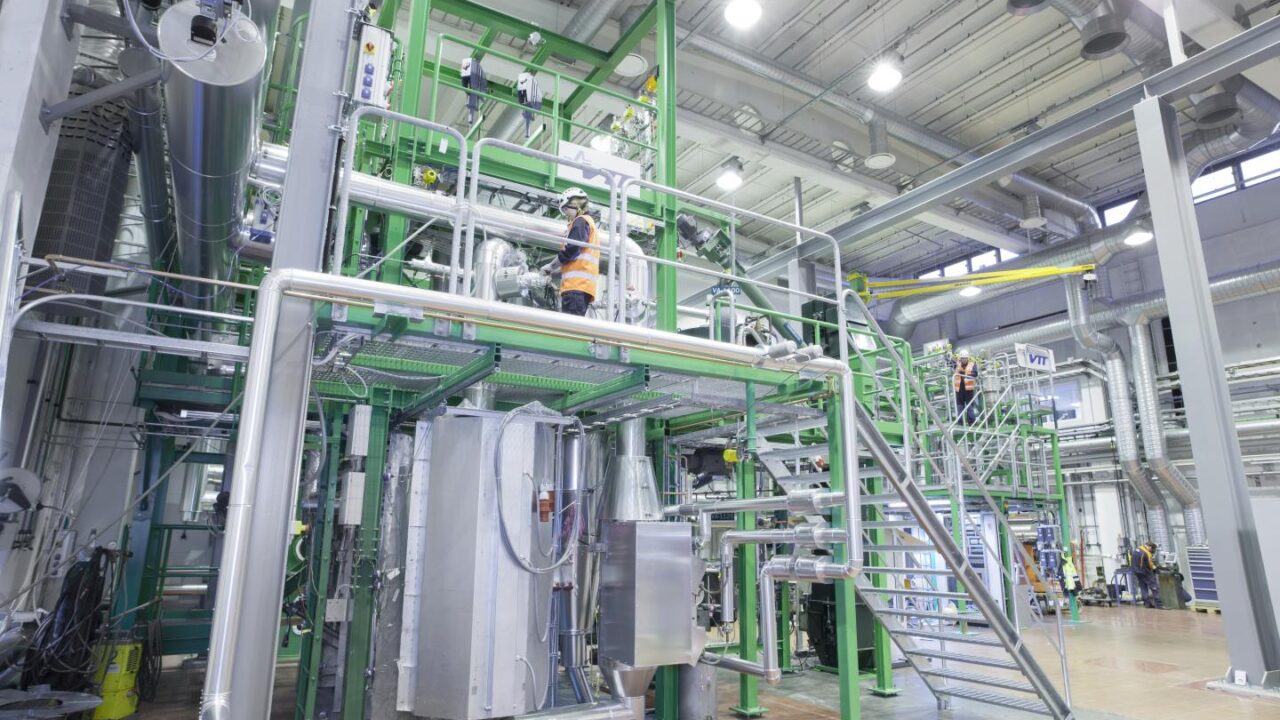
VTT Bioruukki, Finland's bioproducts pilot center in Espoo, is one of the largest in Europe and offers open access. Many companies have their own pilot plants, such as Fibenol in Imavere, where a testing area is located next to the main production line. | Photo: VTT
Developing the bio-based sector: European Commission, entrepreneurs, researchers, and universities
Phasing out oil is, in principle, inevitable. While a decade ago there were (justified) concerns about whether there would be enough wood and other biomass to replace oil, today excellent solutions that reduce oil use in transport and heating are spreading rapidly.
Science has advanced in multiple directions and with greater depth in developing the know-how needed for large-scale bioproduct manufacturing. Unfortunately, bioproducts still struggle to compete on price with fossil-based alternatives. As a result, many bioproducts reach the market in modest forms – primarily as packaging, disposable cups, wrapping materials, and other small-scale applications.
To enable widespread adoption of bioproducts, we must address how to assess and account for their environmental benefits. Replacing fossil-based products with bio-based ones helps preserve fossil carbon underground. At the same time, bioproduct manufacturing and forest regrowth can help reduce atmospheric CO₂ – provided that emissions from the production process are effectively captured.
In addition to a carbon tax, a so-called fossil tax could be introduced on products made from oil or fossil gas. Revenues from this tax could be directed toward the development, production, and marketing of bioproducts – accelerating the transition to more sustainable alternatives.
In the innovation annex to last summer’s European Semester report on Estonia (the EU’s mechanism for coordinating economic and fiscal policy), I highlighted the importance of processing Estonia’s most valuable natural resource – wood – into bioproducts. I also emphasized the need for systematic investment in research and innovation. Wood-related topics fall under the “valorization of local resources” focus area in the TAIE 2035 roadmap (Estonia’s strategy for research, development, innovation, and entrepreneurship).
The European Commission is now more determined than ever to support the growth of the bio-based industry aimed at replacing oil-based products. In March last year, several initiatives were presented to strengthen biotechnology and the bio-based industry in Europe. Commission President Ursula von der Leyen tasked the health commissioner with drafting a European biotechnology regulation. Meanwhile, the commissioner for the environment and circular economy is responsible for preparing a new bioeconomy strategy that will become part of the broader Circular Economy Law.
The EU’s Strategic Technologies for Europe Platform (STEP), which supports innovative investment, also includes the bio-based industry. In addition, the European Commission is facilitating market access for bioproducts by adjusting industrial and internal market rules on standardization and public procurement.
The European Commission is now more determined than ever to support the growth of the bio-based industry aimed at replacing oil-based products.
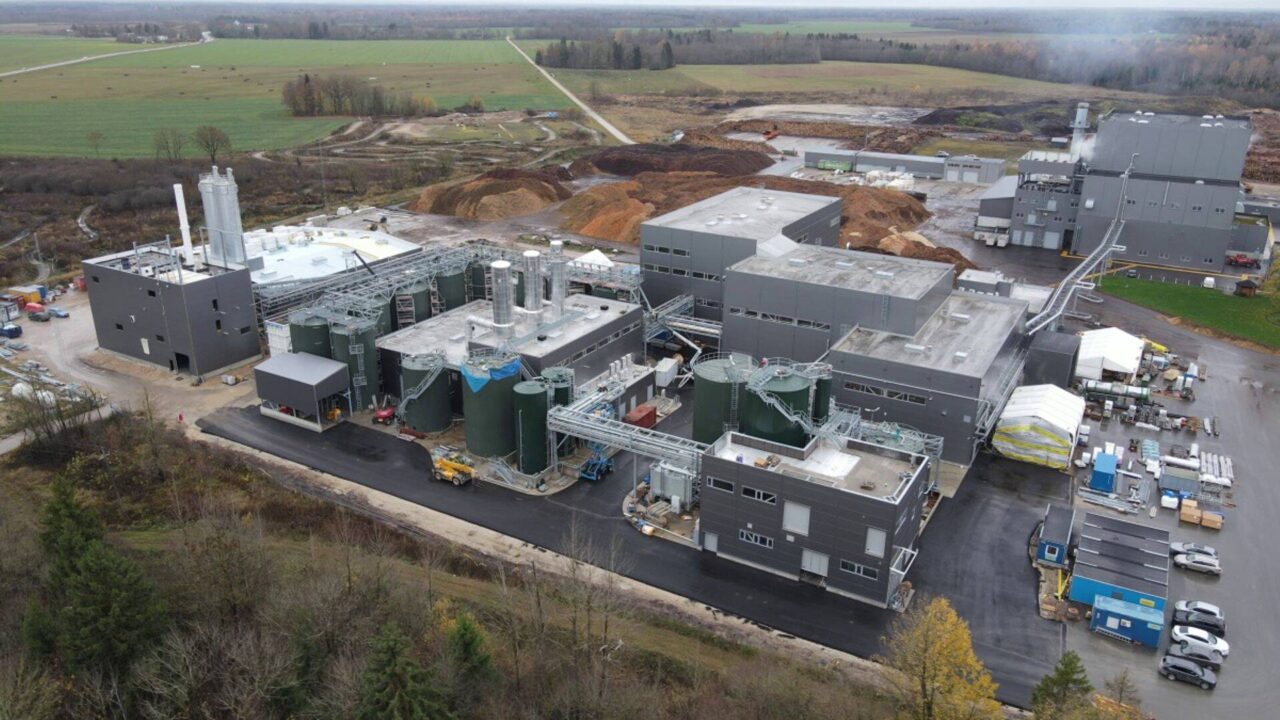
Fibenol's Imavere demonstration plant. | Photo: Fibenol
Estonia’s bio-based momentum is picking up again
Despite a period of stagnation, the era of wood refining and bioproduct manufacturing appears to be gaining new momentum in Estonia. Viru Keemia Grupp (VKG) is planning to build a facility in Lüganuse municipality, Ida-Viru County, focused on the chemical processing of wood and the production of bioproducts. Fibenol, meanwhile, is not limiting itself to its plant in Latvia – if successful, additional facilities are planned elsewhere, including Estonia.
Alongside VKG Fiber and Fibenol, a subsidiary of the Singapore-based Tolaram Group – Horizon, which produces pulp and paper in Kehra –has also recently applied for a contract to purchase low-value state forest timber. Other players have emerged as well: the Norwegian company Biojet, with ExxonMobil as a stakeholder, is planning a green fuels plant in Estonia, while Dutch company Power2X aims to establish a large biomethanol facility in Pärnu.
In the field of bioproduct development, the furthest progress in Estonia has been made by Fibenol, a subsidiary of Graanul Invest. I have had the opportunity to follow their activities closely over the years and have visited their demo plant in Järva County several times.
Fibenol is the most successful Estonian company in securing support from the EU’s Horizon research programme. Through several projects and the European-level joint undertaking, the company has successfully attracted over €20 million in funding – and the success story continues.
At the heart of this progress is Fibenol’s Head of Development, Peep Pitk. The demo plant in Imavere is one of the 16 “flagship” initiatives within the EU’s Circular Bio-based Europe Joint Undertaking, offering a unique and pioneering solution.
Since launching operations, the plant has initiated several new pan-European collaboration projects, enabling Fibenol to bring its products to market. In addition to refining wood sugars, the company is also developing a wide range of lignin-based products with partners –broadening Fibenol’s bioproduct portfolio.
Fibenol is the most successful Estonian company in securing support from the EU’s Horizon research programme.
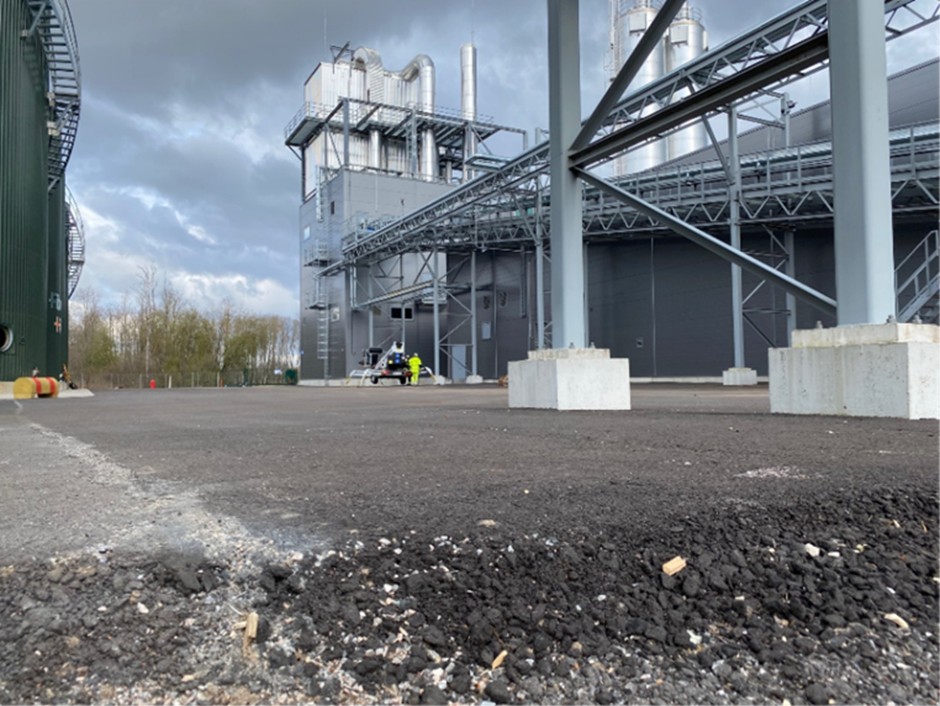
Lignin has been used in the darker section of the asphalt mix at Fibenol's demonstration plant. One might argue whether asphalt is the right place for bioproducts, but the goal is to replace the entire fossil-based economy. | Photo: Jüri Rute
A new generation of bio-innovation: from university labs to industry
Another undeniable success story is Äio, a startup grown out of Tallinn University of Technology. Last spring, I visited their lab, where a group of young scientists are working with remarkable dedication. Äio was recently featured in Trialoog with the headline “Biotech company Äio raised six million euros for a demo plant.” One particularly inspiring idea is the plan to produce food products from wood residues – an initiative being explored in collaboration with Fibenol.
Estonia’s emerging bio-based companies will soon benefit from a new boost thanks to the Applied Research Centre, developing under the umbrella of Metrosert, the Estonian national standards and metrology institute. Already this year, the aim is to establish infrastructure for testing new processes and products – laying the groundwork for a future pilot plant network.
When I visited the bioproduct pilot facility in Ghent, Belgium, I was struck by the immense workload handled by the teams – from preparing funding proposals to hosting training, seminars, and coordinating a pan-European partner network. The message was clear: a high-quality pilot facility requires substantial funding for both setup and operation, which must be sourced from a wide variety of channels.
Estonia’s bioindustry incubator doesn’t need to be simple or cheap –what matters is building a high-quality, sustainable foundation that supports long-term bioproduct and innovation development.
Tallinn University of Technology and the Applied Research Centre are located almost side by side, creating ideal conditions for daily collaboration. TalTech’s research and teaching in wood valorization will be significantly strengthened through deeper knowledge and skills in biochemistry.
Estonia’s bioindustry incubator doesn’t need to be simple or cheap – what matters is building a high-quality, sustainable foundation.
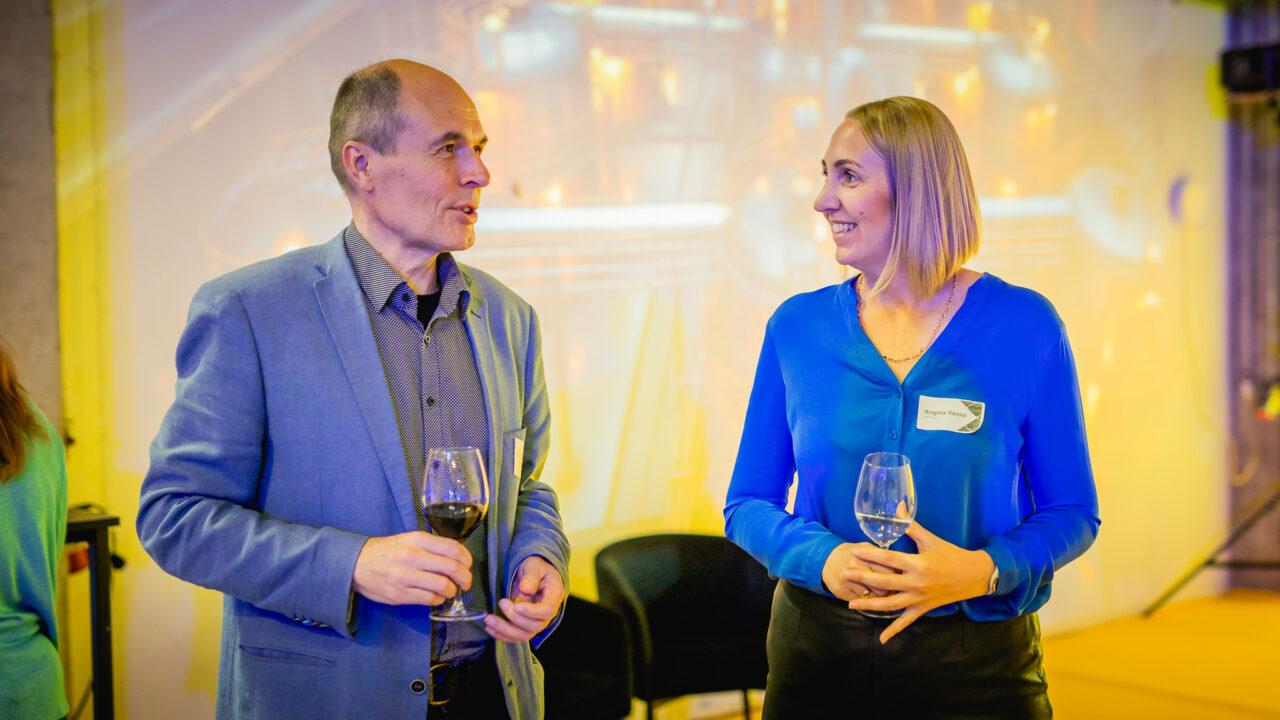
The author (left) at the opening of the Applied Research Center on May 8, 2024, in the future biorefining laboratory at Teaduspargi 8, in conversation with leading biorefining scientist Angela Vaasa. | Photo: Harry Tiits
Estonia’s next leap in bioindustry: enzymes, energy and expertise
As biomass processing evolves, the scientific focus and usable material base expand significantly – particularly because more complex molecules tend to be more valuable. According to forecasts, the next decade will bring an abundance of cheap renewable electricity. This will allow TalTech to begin developing production “recipes” where energy costs no longer limit the creation of complex molecules.
Former TalTech Vice-Rector for Research Tiit Lukk sees enormous potential in lignin: “Wood is composed of three main components: cellulose, hemicellulose, and lignin. While cellulose and hemicellulose are sugar-based polymers, lignin is the world’s largest renewable source of aromatic compounds and a crucial feedstock for the chemical industry of the future.”
Second-generation biorefining
Second-generation biorefining introduces an entirely new approach, where nearly all of the wood is processed – primarily with the help of enzymes – into valuable compounds in specialized facilities. Advancing enzyme-based wood processing could enable Estonia to compete successfully with the long-established wood industry of its Nordic neighbors.
The future growth of Estonia’s wood-based industry, anticipated to occur in the 2030s as cheap electricity becomes the norm, depends heavily on the development work of universities, the Applied Research Centre, and industrial enterprises. This theme was also addressed in the article “We’re all at the starting line of bioengineering” by Mart Loog, Director of the University of Tartu’s Institute of Technology, a leader in EU research funding.
Loog explained that the institute was established under the European Commission’s DigiBio project, which gave it a major initial boost: “DigiBio brings momentum, helps launch and expand the institute, creates new units and labs, and strengthens partnerships.” The institute’s partners include the Center for Biosustainability at the Technical University of Denmark (funded by the Novo Nordisk Foundation) and TalTech’s bioengineering labs.
Advancing enzyme-based wood processing could enable Estonia to compete with the Nordics’ established wood industries.
For Estonia’s emerging bioindustry, scientific breakthroughs will be needed by the end of this decade – possibly even earlier in the case of the planned VKG facility. The range of substances, materials, and products requiring further development is vast. Coupled with declining energy prices and the release of wood resources from combustion, the rise of a new industrial sector will depend most of all on entrepreneurial initiative and long-term vision.
There is, however, one more crucial condition – the competitive price of wood as feedstock. The shrinking timber market, impacted in part by the closure of flows from North Korea’s isolated economy, sets limits on pricing. The bioproducts sector will also need to compete with oil-based chemicals for decades to come, and in some segments, even ultra-cheap coal will remain a rival for longer.
So far, the higher production cost of bioproducts has been the main reason why large-scale replacement of fossil-based products hasn’t materialized. In Estonia, the oil shale industry is also a competitor to the bioeconomy, but its future potential could grow significantly – especially if shale oil is used not for combustion, but as a raw material in chemical production.